Dyeing yarn is a real combination of art and science that has had an important role in development of weaving textiles during the history.
Natural dyes are colorants or dyes derived from plants, insects or minerals that give the yarn special exclusivity that finally add glory, elegance and durability to the handmade carpets and rugs.
The main part of natural dyes are vegetable dyes from plant sources like berries, roots, bark, leaves and wood and other biological sources such as fungi and lichens.
Boustani Glorious Handicrafts let you know more about process of natural dyeing.
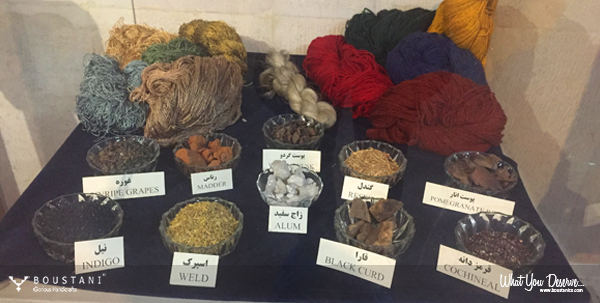
Traditionally the most important natural dye stuffs have been the source of red and blue, the madder root and indigo plant. Madder has been used throughout recorded history, and the plant grows wild in many areas of Iranian Plateau; in other areas it is cultivated as a crop. It is a perennial growing several feet high, and from its thick, pulpy root a substance can be extracted that oxidizes into a red dyestuff. The root does not develop this property until its third year, and after the ninth year the plant is again of little use. The roots are pulled up in the fall and, after dyeing, are ground into a coarse powder. Dyers generally prefer to grind the roots themselves, as the powder is expensive and can be easily adulterated.
The most commonly used dyeing process is to first boil the wool in an alum mordant. Figures for the alum concentration vary, but it is usually given at about ¼ pound for each pound of wool. The mordanting process is usually repeated before the yarn is added to a vat of madder which has previously been prepared by dissolving a weight of the powder nearly equivalent to that of the wool. The amount of time in the dye depends upon the desired shade, usually several hours; then the yarn is rinsed thoroughly, preferably in a running stream. Variations in technique may produce hues of widely differing character, as, for example, in the process formerly favored in the Arak area, Iran. The characteristic rose color was produced by leaving the wool for two days in a bath of madder and whey, followed by scouring in running water for 24 to 48 hours.
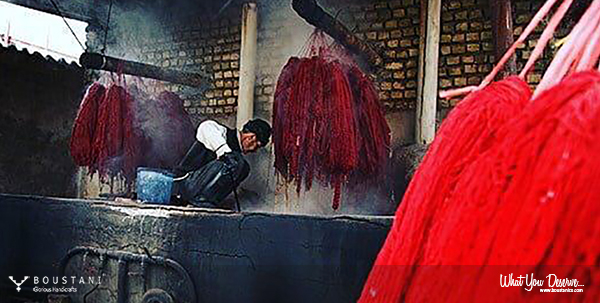
Indigo presents a slightly different problem, as it is not widely grown in the Middle East, and most of it must be imported from abroad. The synthetic has almost completely replaced the natural substance; its use is a simple process involving sodium hydrosulfite. The older is quite complex: indigo is fermented with clay, slaked lime, sugar, and potash. The basic mixture takes several days to prepare, but the efforts are justified by the enormous range of blues that may be obtained. There are some who maintain that the same results are possible using the synthetic indigo with the old fermentation method. The added difficulty, how-ever, makes this unlikely.
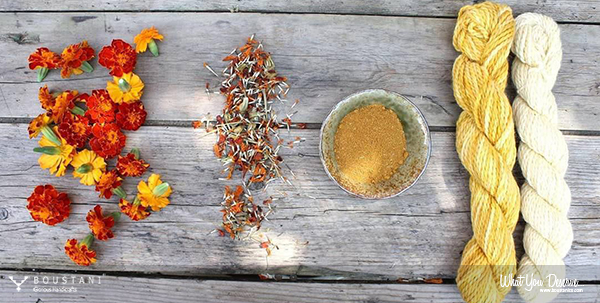
Shades of orange are frequently dyed with henna laves, but there is much variation; vine leaves and madder will also produce a good orange. Black has presented probably the greatest problem to the dyer, as one would judge by number of carpets with this color worn off. The easiest solution is to use naturally dark wool, although this is not always available. (Some sources indicate that dark wool does not wear so well as white, but this seems unlikely.) In some areas dark wool may be dyed with indigo, producing a particularly deep, rich shade. Most other blacks are unsatisfactory for a number of reasons. The black from oak bark contains a high concentration of iron salts, which weaken the wool and make it brittle. Among the earliest aniline dyes was a black so acidic that it severely damaged the fibers.